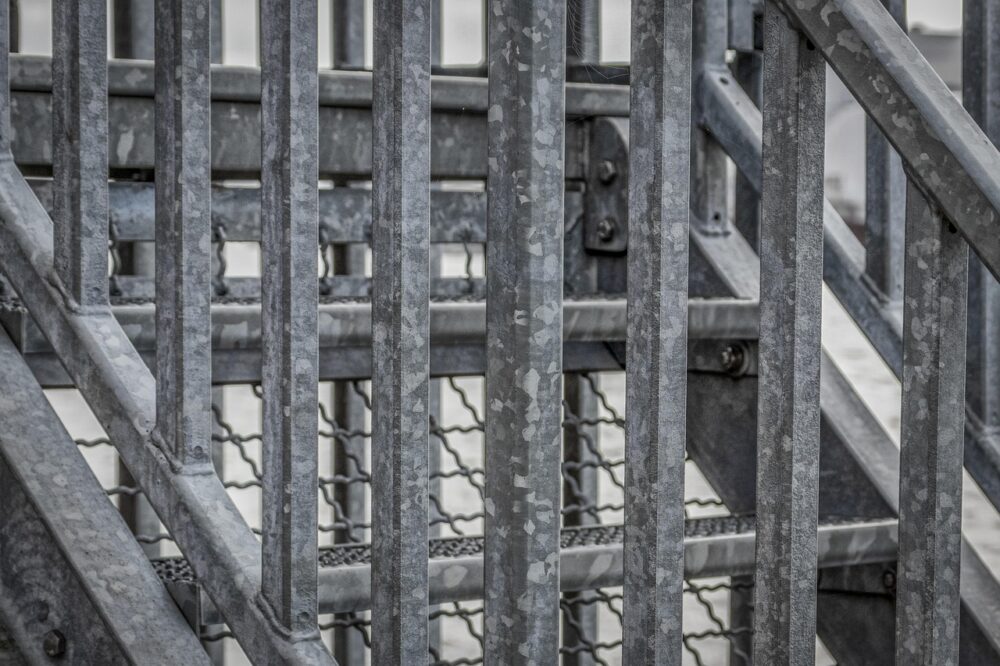
表面処理の基礎:溶融亜鉛メッキ
溶融亜鉛めっきは、鉄や鋼の表面に溶融した亜鉛の皮膜を形成させることで、優れた耐食性を付与する表面処理技術です。古くから用いられてきた信頼性の高い防錆方法であり、建築構造物、道路設備、電力設備、通信設備、農業用設備、自動車部品など、屋外や腐食性の高い環境で使用される鉄鋼製品の長寿命化に不可欠な技術です。
その名の由来は、処理する鉄鋼製品を溶融した亜鉛の浴槽に文字通り「漬け込む」という工程にあります。このシンプルな工程によって、鉄鋼表面全体に均一で密着性の高い亜鉛皮膜が形成され、長期間にわたり錆から保護します。
溶融亜鉛メッキのプロセス
溶融亜鉛めっきのプロセスは、一般的に以下の段階を経て行われます。まず、鉄鋼製品の表面に付着している油分、錆、スケールなどの汚れを徹底的に除去する前処理が非常に重要です。これには、酸洗(塩酸や硫酸などの酸溶液に浸漬)、脱脂(アルカリ溶液などを使用)、水洗などの工程が含まれます。前処理が不十分だと、均一で密着性の高いめっき皮膜が得られず、耐食性の低下につながります。
次に、フラックス処理が行われます。これは、鉄鋼表面に残存する酸化物を除去し、溶融亜鉛との濡れ性を向上させるための工程です。塩化亜鉛アンモニウムなどのフラックス溶液に浸漬または塗布した後、乾燥させます。
次が溶融亜鉛めっきの本工程です。フラックス処理された鉄鋼製品は、約450℃程度の高温に保たれた溶融亜鉛の浴槽に浸漬されます。この時、鉄と亜鉛が金属間反応を起こし、数層の合金層と最表層の純亜鉛層からなる強固なめっき皮膜が形成されます。浴槽から引き上げられる際、余分な亜鉛が除去され、均一な厚さのめっき層が得られるように調整されます。
めっき後の後処理として、冷却が行われます。自然冷却のほか、水冷や空冷が行われることもあります。また、必要に応じて、めっき皮膜の保護や外観の向上を目的とした化成処理(クロメート処理など)や、塗装が行われることもあります。
溶融亜鉛メッキのメリット
溶融亜鉛めっきの最大のメリットは、その優れた耐食性です。亜鉛は鉄よりもイオン化傾向が大きいため、鉄よりも先に腐食されることで鉄を守る「犠牲防食」の効果を発揮します。たとえめっき皮膜に傷がついて鉄が露出した場合でも、亜鉛が優先的に腐食されるため、錆の進行を抑制することができます。また、めっき皮膜自体が緻密で不動態化しやすく、物理的な保護膜としても機能します。
さらに、溶融亜鉛めっきは、比較的安価で耐久性に優れており、一度の処理で長期間にわたる防錆効果が期待できます。塗料のように定期的な塗り替えの必要が少ないため、メンテナンスコストを低減することができます。
溶融亜鉛メッキのデメリット
一方で、デメリットとしては、高温の溶融亜鉛に浸漬するため、製品の形状やサイズに制約があること、めっき時に亜鉛のドロスやスパングルといった特有の外観が生じる場合があること、精密な寸法管理が難しい場合があることなどが挙げられます。しかし、これらの点は技術の進歩によって改善されつつあります。
このように、溶融亜鉛めっきは、鉄鋼製品の耐食性を向上させるための極めて有効な手段であり、社会インフラや産業設備の安全・安心を支える重要な技術として、今後も広く活用されていくと考えられます。
コメント